About the project
MobileRobot - Development of an omnidirectional manipulator for a mobile robot welding system with demo application in automated welding
The aim of the "MobileRobot" project is to develop a mobile robot consisting of an omnidirectional mobile platform and a robot arm that moves continuously in space while processing a workpiece. This means that even very large workpieces can be processed continuously. The mobile robot is used for processing and measuring tasks such as surface grinding, painting, testing or welding.
In contrast to existing solutions, a combination of robot and omnidirectional mobile platform is implemented to form an overall kinematic system, so that - in contrast to previous systems where mobile platforms are only used to position robots or workpieces - a joint and synchronous motion control takes place, incorporating the three degrees of freedom of the mobile platform into the overall concept. The combination of the two systems at control level results in significant advantages in terms of movement, as the additional degrees of freedom allow a large number of different movement sequences for the same path and the workspace is considerably extended. Depending on the problem (minimum time, energy consumption, stability with handling weight, etc.), an appropriate path can then be selected. In addition, it is possible to react interactively to external influences (objects in the path) while the path is being processed, without deviating from the path of the Tool Center Point (TCP).
By synchronizing the omnidirectional platform and robot arm in real time, processing can take place while the platform is moving along the workpiece. The TCP of the mobile robot is moved along a path along the workpiece by synchronizing the movement of the platform and arms in real time and by sensory detection of the absolute position of the mobile platform using a laser scanner and detection of the relative position of the TCP of the robot arm to the workpiece using sensors. In order to enable low-vibration machining, the omnidirectional platform is realized by means of rotary/steering drives. The rotary/steering drives each consist of two independently driven wheels that move around a central steering axis. The project is investigating how the kinematic limitations of the rotary/steering drives can be taken into account in motion planning and control.
Sponsor
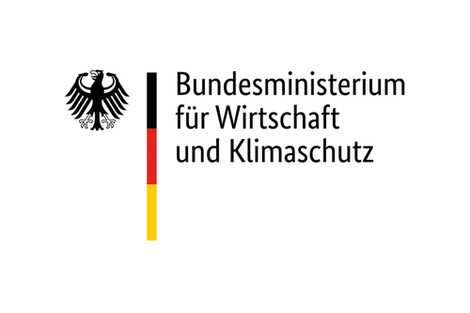
Funding code
KK5119001BD0
Cooperation/project partners
- GD Engineering & Automation GmbH
- Institute for the Digital Transformation of Application and Living Domains (IDiAL)